INFRASTRUCTURE
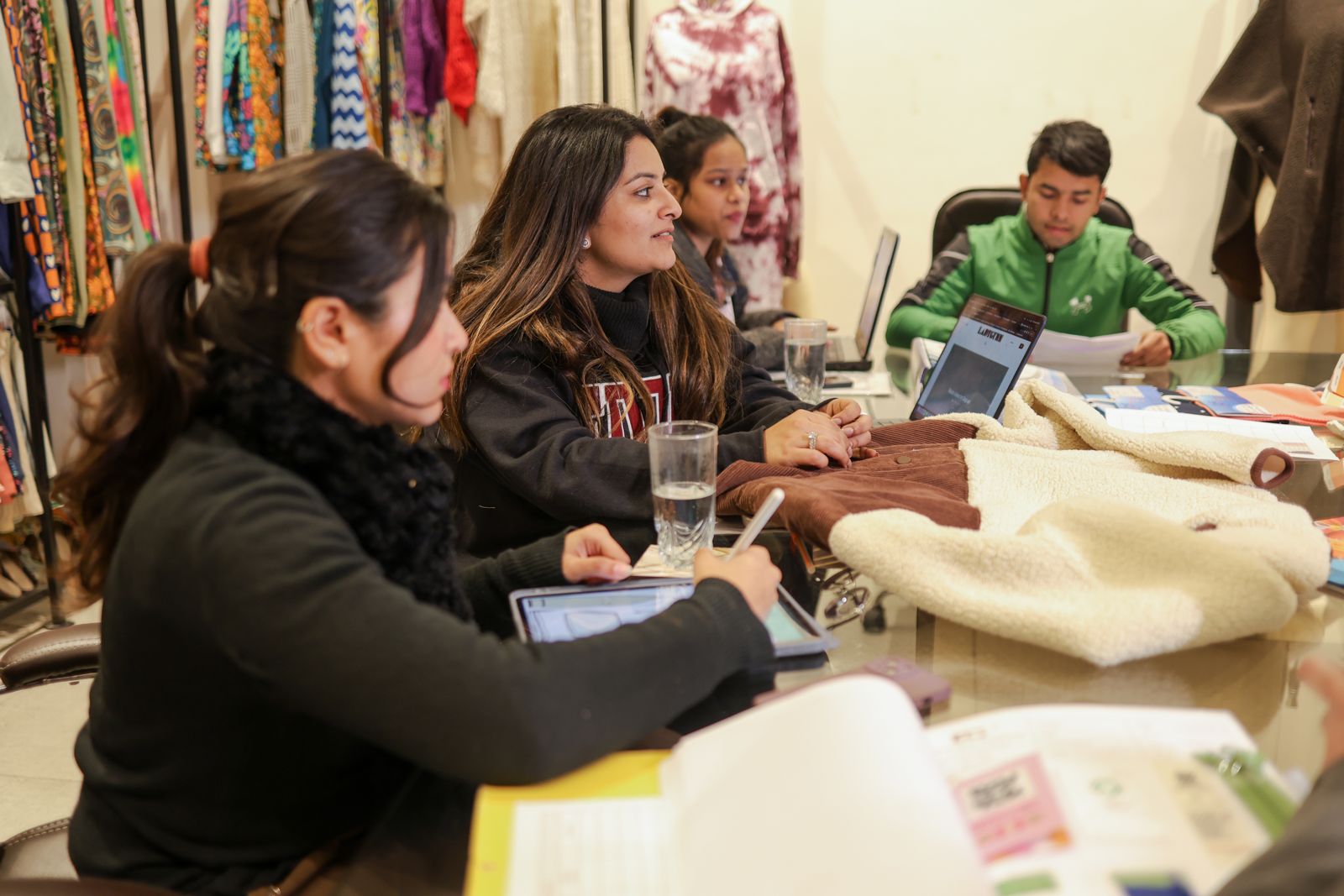
DESIGN & conceptualization
Based on market insights and client requirements, designers receive a creative briefing that outlines the project objectives, target audience, design direction, and any specific themes or concepts to be incorporated into the collection.
Once the design concepts are finalized, designers work closely with the sourcing team to select appropriate knit fabrics for the collection. Factors such as fiber composition, weight, stretch, drape, and texture are considered to ensure that the chosen fabrics align with the design vision and desired garment properties.
PATTERN MAKING
Patterns for the knitwear garments are created based on the finalized designs. Pattern makers use specialized techniques to develop patterns that take into account the unique properties of knit fabrics, such as stretch and recovery. Prototypes or samples of the garments are then produced for fit testing and evaluation.

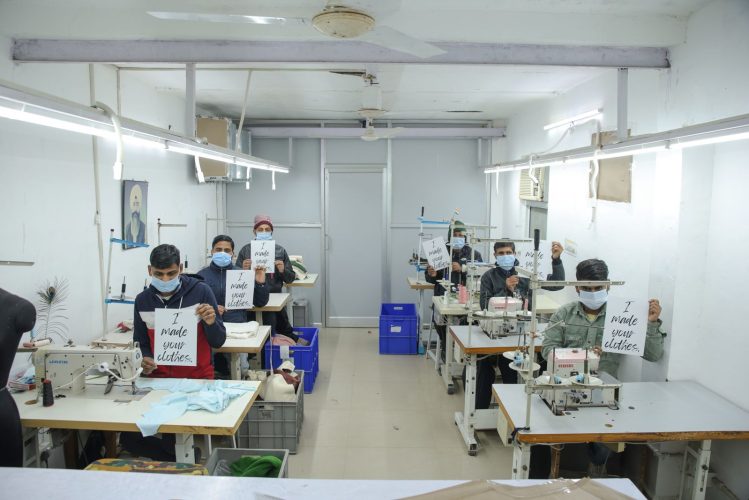
SAMPLING
The sampling process involves creating prototypes of the garments based on the finalized patterns and fabric choices. Skilled sample makers or prototype technicians cut and sew the fabric according to the specifications provided, assembling the garments for evaluation.
Once the samples are made, they undergo fit sessions where they are tried on by fit models or mannequins. This step allows designers and fit technicians to assess the fit, sizing, and overall look of the garments.
FABRIC CHECK
Inspectors carefully examine the fabric for various types of defects, including stains, holes, tears, snags, discolorations, and knitting flaws. They also check for print or dye irregularities, such as smudges or misprints.
If the fabric is dyed or printed, inspectors compare the colour of the fabric to a reference standard or swatch to ensure colour accuracy and consistency. Any deviations from the standard are noted for further evaluation.
After inspection, fabric rolls are graded based on their quality for production requirements. Rolls that meet quality standards are designated as first quality and proceed to the cutting phase. Rolls with minor defects may be designated as second quality and used for less critical applications.
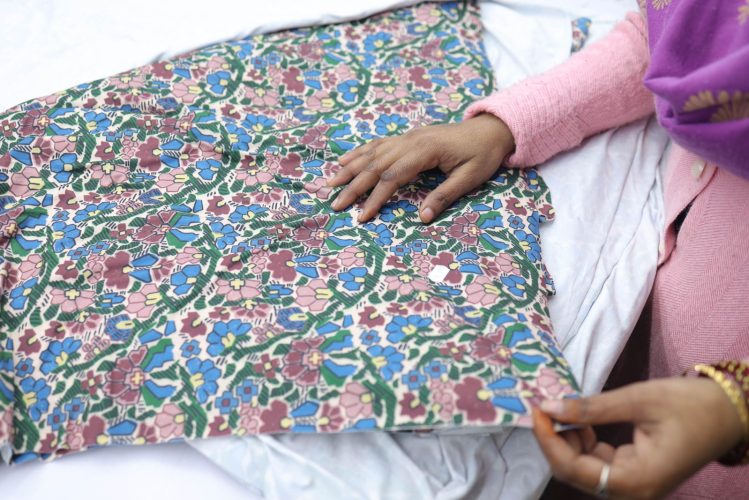
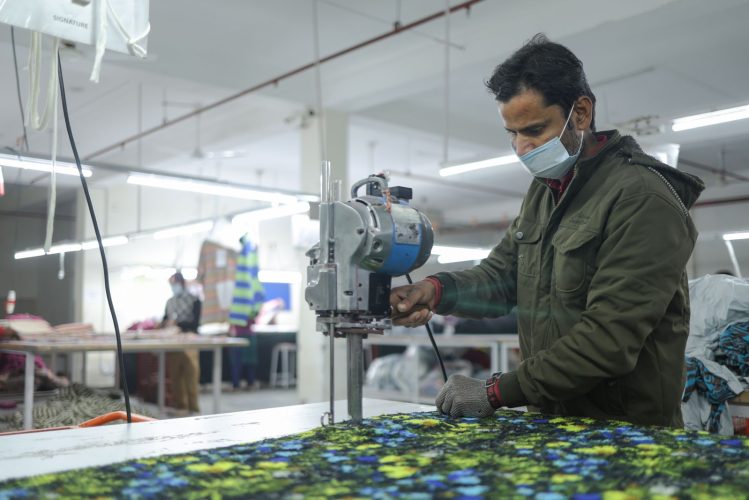
CUTTING
We are equipped with 10 cutting tables & have a capacity of cutting 8,000 pcs daily. Trained operators, perform the cutting process. They meticulously follow the outlines of the patterns, ensuring accuracy and consistency in cutting each garment piece.
Specialized cutting techniques may be employed to minimize distortion . Techniques such as single-ply cutting or stack cutting are used based on the requirements of the production run.
Throughout the process, quality control measures are implemented to check for any deviations from the specified dimensions, irregularities in cutting, or defects in the fabric.
CUT PANEL CHECKING
After the cutting process is completed, the cut garment panels are collected and organized according to size, style, or other relevant criteria.
A dedicated inspection area is set up, equipped with adequate lighting and space for inspectors to examine the cut panels closely.
Each cut panel is visually inspected for various defects and discrepancies, including, straightness, shape, size, dimensions, notches, markings & fabric quality.
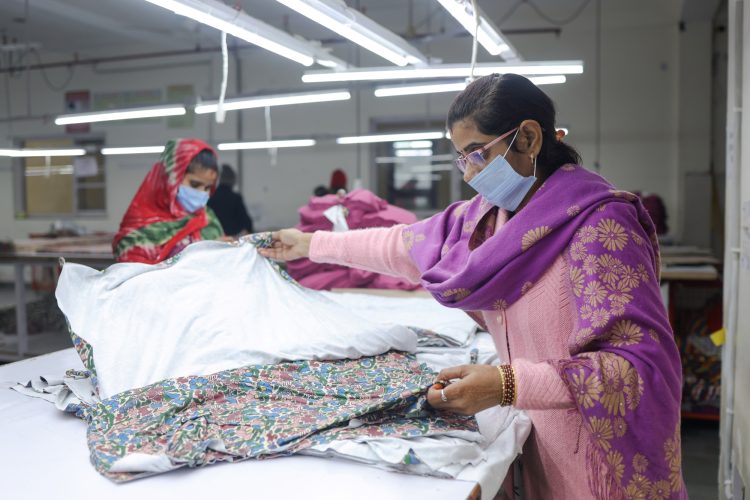
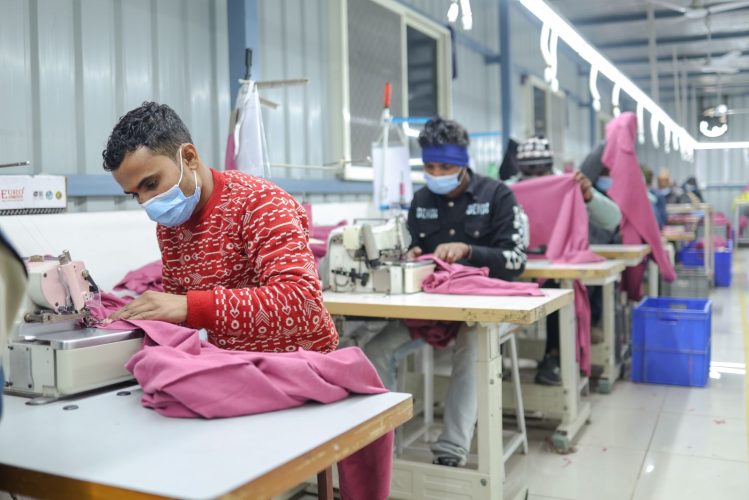
STITCHING
Before sewing begins, a stitching plan is developed based on the garment design, fabric type, and construction requirements. This plan outlines the sequence of stitching operations, stitch types, thread colors, and any special techniques or features to be incorporated.
We are equipped with overlock machines, civerstitch machines, flatlock machines & specialised machines used for specialized techniques such as binding, gathering etc.
Our unit is equipped with 200 machines and have a capacity of creating 5,000 pcs daily.
THREAD CUT
Trimming excess threads and yarns is one of the initial steps in the finishing process. Skilled workers carefully trim any loose threads or excess yarns left from the stitching process, ensuring a neat and tidy appearance for the finished garment.
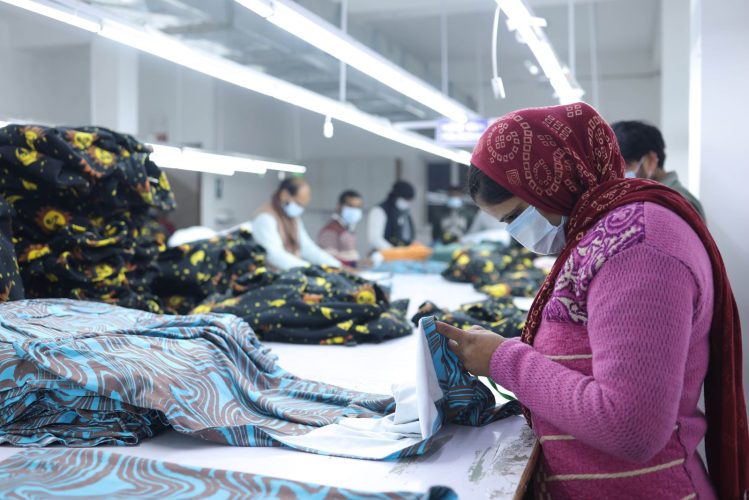
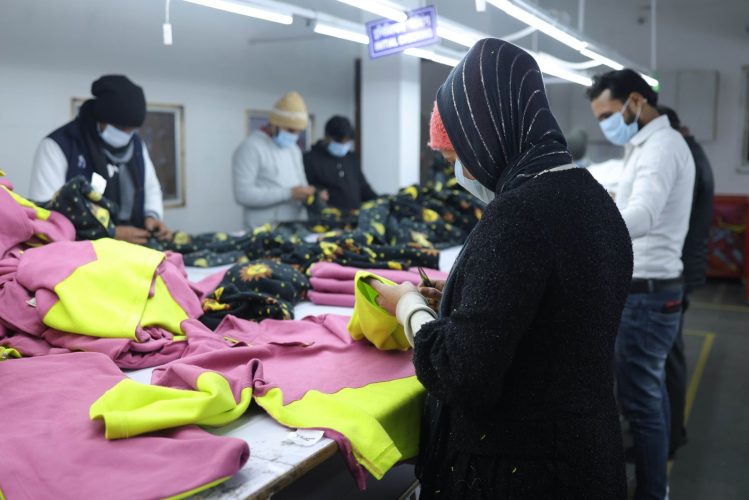
FINISHING
Trained inspectors examine each garment for defects such as loose threads, stitching irregularities, fabric flaws, or incorrect sizing. Any issues identified during this inspection are noted for correction.
Further garments are garments may undergo pressing or ironing to remove wrinkles and creases accumulated during the sewing process.
Any remaining loose threads or excess seam allowances are trimmed, and thread ends are securely fastened to prevent unravelling or fraying. This meticulous attention to detail ensures that the garments maintain their quality and appearance over time.
FINAL INSPECTION
Finished garments are gathered from the production line or finishing area and organized for inspection.
Inspectors examine each garment for visual defects such as loose threads, uneven stitching, fabric pulls, stains, discolorations, or printing errors.
Seam integrity is assessed to ensure that stitches are secure, straight, and evenly spaced.
Garments are checked against measurement specifications and fit samples to ensure accuracy in sizing and proportions.

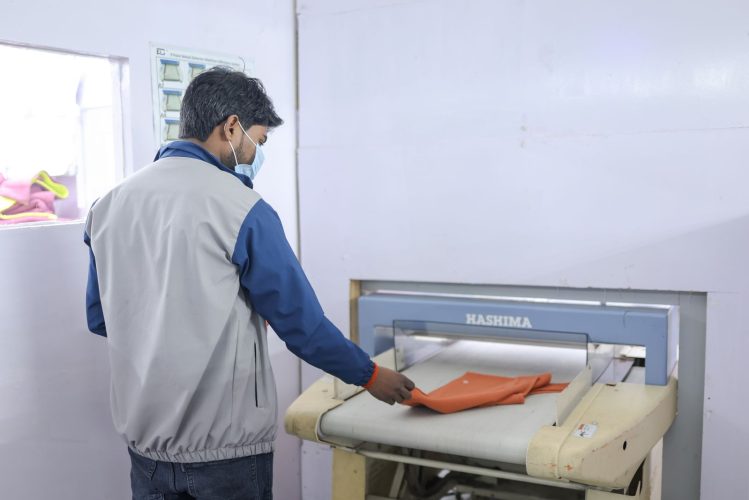
NEEDLE CHECK
We have a total of 10 cutting tables and a capacity of cutting 6000 pieces per day.
Cutting tables are equipped with cutting tools such as straight knives. Skilled operators use these tools to cut along the outlined patterns, ensuring precision and minimizing fabric wastage.
PACKAGING
We have a total of 10 cutting tables and a capacity of cutting 6000 pieces per day.
Cutting tables are equipped with cutting tools such as straight knives. Skilled operators use these tools to cut along the outlined patterns, ensuring precision and minimizing fabric wastage.
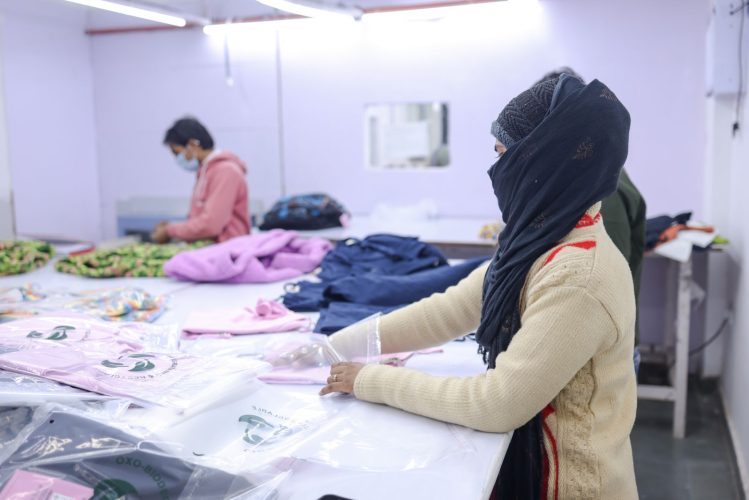